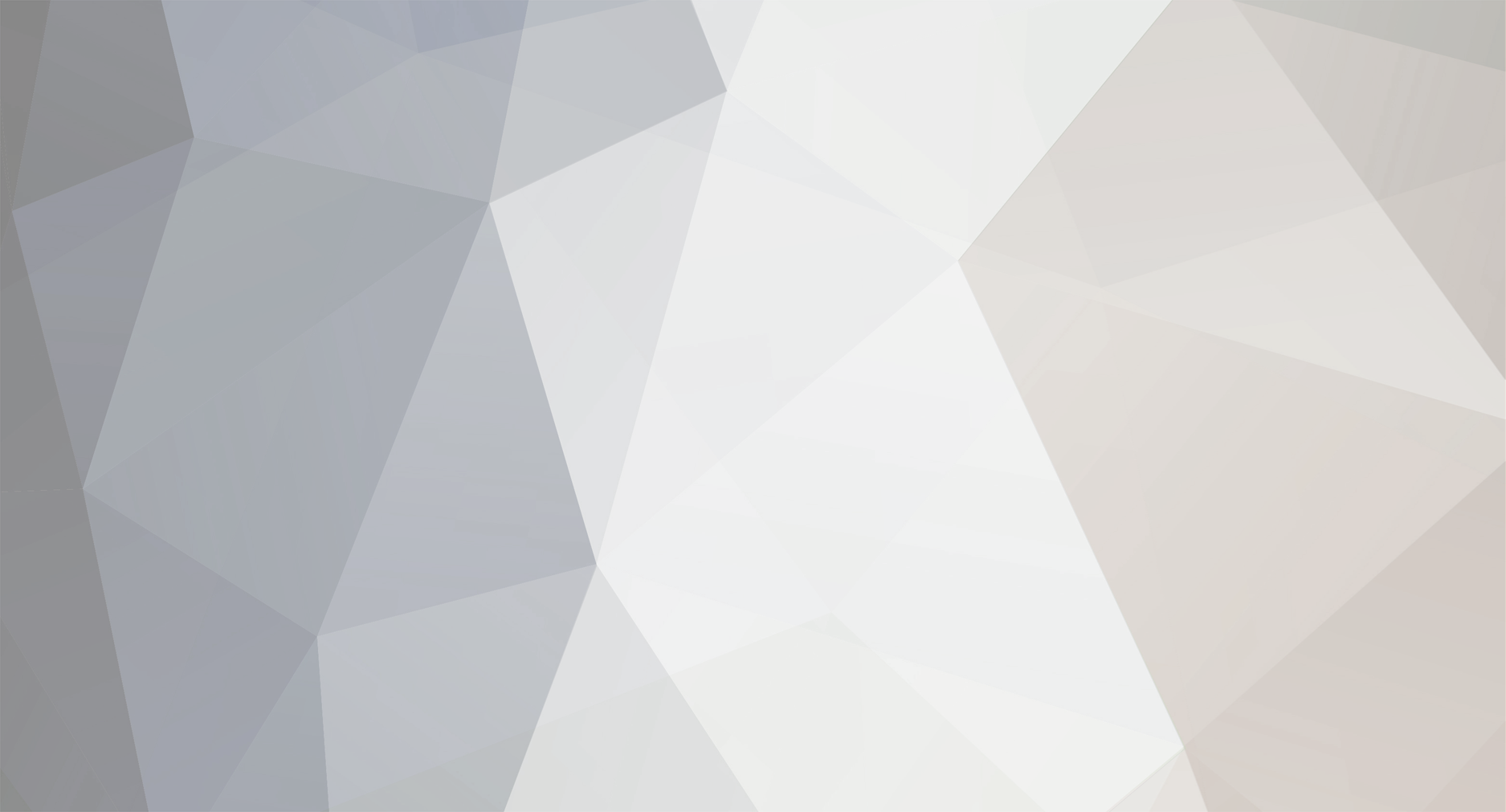
patternmaker
Member-
Posts
23 -
Joined
-
Last visited
Content Type
Forums
Calendar
Gallery
Everything posted by patternmaker
-
Keeping sharp edges on imported Rhino model
patternmaker replied to patternmaker's topic in General 3DCoat
Thanks! I knew you could print discrete objects inside each others, like a ball in a cage, but didn't know objects could touch or overlap. I check my polysurfaces in Rhino pretty carefully. Took quite a while to clean this one up. The picture shows a place where in 3DCoat surface mode passing over it with a smooth or build tool would cause a really long, spiky eruption to occur. Looking at it in wireframe showed little folded up surfaces bunched together. Could this be a tolerance issue? I try not to build at a tighter tolerance than the printer will work to; in this case, I used .003". Any suggestions for how to fix these things when they do occur? There were about five or six places where this happened on this model. Sorry not to show the full model - that would violate my customer's confidentiality. -
Keeping sharp edges on imported Rhino model
patternmaker replied to patternmaker's topic in General 3DCoat
Thanks for the advice! I did get a more usable surface by meshing finer in Rhino, but I also found that I could improve my original mesh by scaling up a bit less than I was, then subdividing when merging. Subdividing twice generally crashed the program. Having a lot of trouble now getting objects to merge with this one in surface mode. Looks like I will need to switch everything to voxels after all, merge all the parts, then clean up the whole assembly back in surface mode. Needs to be one unit for 3d printing. In surface mode, I had quite a few places where lots of triangles meet at a point, and they sometimes had messy little bunches of triangles hiding inside at those points. Got rid of them by smoothing, decimating, reducing, reconstructing using "clean clay", but it was not easy. Reconstruct would often cause a crash. Is there a better way to do that? I'm guessing those types of bad triangles were what was making my objects not want to boolean sometimes. -
Keeping sharp edges on imported Rhino model
patternmaker replied to patternmaker's topic in General 3DCoat
I can get closer by voxelizing, but then must sharpen all the edges again manually (with pinch or crease?). It stays sharp if I merge it as a surface model. Do I need to export a much finer mesh from Rhino in order to be able to work with the edges? I was hoping there was some command in 3DCoat that would let me break up the large polygons in the surface model without damaging the sharp edges. Is there nothing that does that? Many thanks for your replies! -
Keeping sharp edges on imported Rhino model
patternmaker replied to patternmaker's topic in General 3DCoat
You mean small as in number of polygons, or in actual size? Actual size model fits in your hand. Surface model has about 1.2 million polygons at this point. The detail area shown would be about 1cm square in actual product size. -
Keeping sharp edges on imported Rhino model
patternmaker replied to patternmaker's topic in General 3DCoat
Sorry, didn't attach the pictures I referred to correctly. They should be there now. -
I am trying to make more polygons in surface mode (voxel room) on the sharp - edged object shown so I can blend it in with other sculpted objects that are merged with it. I can't seem to find a way that doesn't collapse the edge polygons as shown. Is there a recommended brush or settings that will let me do this? Right now, if I get too close to the sharp object with any smoothing brush, it "melts" the edges badly. The sharp object was modeled in NURBS, then exported as an obj. I imported it into 3DCoat with "merge without voxelizing" checked. It is a fairly complex object and was over 500,000 polycount, even at the resolution you see. I have been successfully merging other sculpted surface objects to it without damaging the sharp edges. Just need to be able to work on the intersections. Many Thanks! Dave
-
Many thanks! I will probably go with your advice. I am using 3D coat more and more, but just for sculpting, so painting 3d models is not a big concern. I use CS6 for making "pencil" sketches of products that later get modeled in 3D coat. Haven't been able to slow CS6 down even with my current setup, but 3D Coat will definitely slow down after a while with bigger brushes. So I guess that is my main reason for upgrading.
-
I'm building a new computer and want to know if anyone has determined whether it is better to use a quadro card, like the 4000, with 256 CUDA cores, or something like the GeForce GTX 680, which has 1536 CUDA cores. I would also be using Rhino/Flamingo and CS6 . I found just a bit in earlier topics that would suggest that 3D Coat was not yet optimized for the latest CUDA, so that the greater number of cores in the GTX 680 might not be that much of an advantage over whatever it is that makes the quadro cards so expensive. Anyone got any advice about this? Many Thanks!
-
Lots of great info, thanks! Wacom probably won't like this, but I think it makes more sense for my purposes to get the regular 24HD based on your experience and thoughts. I'll most likely order one next week.
-
Thanks for the quick response! I will probably get the "older" 24HD and take my chances on regretting that decision in a few years if the touch version gets fully supported. I recently got a GeekDesk and have been working standing most of the time. Much better for my back. I'm expecting to use the cintiq in a nearly flat position with the table kind of low. Might need to make some extra platforms for keyboard, mouse, and spaceball. I can't picture working without a spaceball, though like you are doing. I think it at least doubles my efficiency because of how quickly I can orient my model. Hoping the 24HD will have a similar efficiency boosting effect by giving me better hand control. In your experience is touching the pen right on the model instead of on a tablet like an Intuos much more efficient? I'm also hoping it will allow me to sculpt and draw with smoother movements because of the larger surface and being able to see where my hand is and use natural arm motions. Is this true in your experience? I use Sketchbook Pro a lot for presenting concepts and am hoping I can actually use plastic french curves and straight edges right on the 24HD to guide the pen. Maybe even use them sometimes in 3D Coat to sculpt features that follow a curve more smoothly (?) Will that work like I'm hoping?
-
Great to get some responses to this! Thanks! I'm wondering, BeatKitano, if you use a 3dconnexion device, and if so, where you put it when you use the 24HD. That was probably my main concern and reason for wanting the 24HD touch. I'm used to working with a Wacom Intuos tablet and a spaceball, but both are on the desk at the same level. The 24 HD moves your working surface to a very different position, especially if it is used flat. Seems like the spaceball could be hard to reach, or at least different enough in position to require retraining your hand to use it well. Regarding implementing support for the Touch, it looks like even Autodesk hasn't decided it is a high enough priority for Mudbox or Sketchbook yet. These are so expensive that I would expect relatively very few will get sold, so am I right that it could be a very long time before we could expect 3D Coat to support this?
-
I'm considering getting one of these, http://www.wacom.com/en/Products/Cintiq/Cintiq24touch.aspx but probably only if 3DCoat is planning to add support for the gesture feature. I would want to be able to use that instead of my usual spaceball. Should I expect support for it to be months away or years away, or what? It looks like only Corel Painter 12 actually supports it right now.
-
Thank you! I will leave it alone and not worry, then!
-
Sorry to not understand, but by "Yep", do you mean I SHOULD be able to change the 32 to 336? Are CUDA cores logical CPUs? Thanks!
-
In the "preferences" menu, there is an entry "Max processors to be used". Is that supposed to match the number of CUDA cores on your video card? It lists 32 as the default number (?), but my card has 336 cores (GTX 560). If I change the number to 336, it changes back to 32 if I close the preferences menu and reopen it.
-
The metal printing process still has a way to go before it can compare to real molten metal casting. Along with layer lines that may need to be blended, I have seen bad adhesion between layers. That was a few years ago, but due to an improperly adjusted machine, I think, not the basic concept of the process. The end product is not really solid metal like a casting. It is a fused together powder, though it may be getting pretty close to a solid material these days. Investment casting (lost wax) will get you the best quality surface for sure, though, as I said, it is not cheap. Sand casting can be the cheapest way, but only if you are able to make the original pattern correctly for the foundry, and the surface will not be as good as an investment casting. As far as other materials go, not all investment casting foundries will do brass. It requires more careful melting control because it can easily overheat and burn off zinc, which changes the composition and can create lots of problems. It oxidizes more readily than most bronzes and so, is "dirty", and can get surface defects easily when casting. A foundry that knows how can do it, though. A major negative for brass is that it is very hard to weld (because of the zinc content). Pewter is a very low melting temperature alloy. You can pour it into a silicone mold, so it would be a waste of money to investment cast it. The metal itself is fairly expensive, though. Real pewter contains a lot of tin, which, contrary to what you might think from the old phrase "tin can" (actually "tinned can"), is one of the most expensive non-precious metals. Smelters often keep their tin ingots in a safe! There are a variety of bronzes, though most art foundries use silicon bronze, mostly because it is easy to weld and fairly easy to cast. Hope this has been helpful.
-
If you want a real metal piece, that is probably the easiest route. Search for foundries that do sculpture or art casting. Your original does not need to be wax, in fact, it is better if it isn't. The foundry will want to make a rubber mold from your original because the first casting often does not work, so you'd lose everything if you used your only wax. You probably only need to have the face side for this. The art foundries typically would paint wax into an open rubber mold of a shape like yours and build up its thickness that way. Sometimes they do the equivalent of ceramic slip casting: fill the mold with wax, wait for a surface skin to form, dump out the excess when it is thick enough. Industrial foundries will demand a complete mold (front and back) and usually inject wax into it, much like plastic injection, so that method would be too expensive for you to use. You mentioned "client" in your last entry. If this is for someone else, you had better make sure they are ok with the plastic substitute method I described. If they think you are giving them bronze and they get bronze-filled plastic...! anyway, you could make it work, but should probably reinforce the knocker handle with an internal metal piece, and put another piece of metal where the handle will hit. Just put the metal pieces in the rubber mold before filling it with the fake bronze (sometimes called "cold-cast bronze"). The main "head" part should be cast as a solid flat-backed chunk - no hollowing. You may also want to cast in some threaded inserts for mounting screws. I do not sell materials myself. Look at http://www.smooth-on.com/. You could make this yourself at home with these materials and mass produce it that way if you wanted to. Only one warning: test the materials to make sure they don't interact badly before making a mold of your original. Sometimes the materials can refuse to harden, or etch your surfaces, or refuse to come apart after casting!
-
Haven't had time to check into the forum in a while - this is in my field, so I thought I'd reply. First, that is really big for a doorknocker! Is it 18 inches or 18 centimeters tall? $5500 doesn't sound bad for a metal printing 18" tall. Who did you find with a machine that big? Anyway, sand casting is the cheapest way to do this only if your time is cheap or free, and you know what you are doing and can make what the foundry needs to do the job. You could get this printed in some kind of plastic and hand work the result so it would be usable. FDM would be cheap enough, maybe at that size, but you will need to put in a lot of work smoothing it out, not just knocking down ridges, but actually filling in negatives, too. Other 3D printing methods will cost more and still require hand work. Sand patterns need to be quite smooth, and definitely well drafted (tapered in the direction the mold separates), preferably at least 5 degrees for something like this. Z corp models would need to be used to make more durable models by making molds and new plastic positives, usually cast polyurethane, because they are too fragile to use in a foundry. If you really want to go this route, aim for a uniform wall section of about 3/16", no less than 1/8", and no more than 1/4". That rule of thumb applies whether it is 3" tall or 30" tall. Have it made in silicon bronze, preferably everdur, which welds easily, since the casting will almost certainly need weld repair. Realize that the casting will be about 1-1/2% smaller than your pattern. If you make just what you've shown, it would be called a "loose" pattern, and many foundries will not use those. They may also not like you to ask for just one, but if they are hard up for work, which many are these days, they may do it for a few hundred dollars. The resulting casting will likely be fairly rough textured and will need a lot of hand work to get it smooth, but if you don't mind the texture, maybe you could use it to your advantage. Shadows in deep areas will be darker and make the sculpture look even deeper than it really is. As to waxes and investment castings - the process is much more expensive, but art foundries are more used to stuff like this than sand foundries, so they would help you more with it. Probably charge you several thousand, though, even after you have made a "perfect" original for them to use. Commercial industrial investment casting foundries will want nothing to do with this type of thing. If you just want this to be functional for your own use, you might want to just get it printed as cheaply as possible, smooth it out yourself, make a rubber mold from it (Smooth-on makes fairly cheap materials), then cast a bronze-filled epoxy or urethane into the mold. I've seen a number of sculptures done that way, and they look OK. Anyway, nice job modeling! Sorry if I don't reply to this thread in a timely way after this - really very busy right now, just saw this on my lunch break and thought I'd make a few points. Best of luck!
-
I'm getting closer to my goal here, but still having problems. I've found that I should import the objects one at a time. They seem to scale correctly and locate correctly, but not always. Out of a group of 7 objects, 4 imported exactly right, 2 imported right size but wrong location, and one imported wrong size and wrong location. Here is my sequence: 1) select a main layer 2)from the "file" menu, select "merge object" 3) in the merge dialogue, with "merge to separate volumes" checked, I click "autoscale" then "subdivide" then "apply". 4) I click "grow" to finish merging the layer 5) I go back to file menu, repeat from step 2 The objects all appear in their own layers below the main layer as I think they should. What should I do differently to get all the objects to import right? Thanks!
-
Thanks very much for your reply! Do I understand that for this to work the way I want, I will need to make just one obj file that contains all the models, then use the "merge to separate Objects" command? In other words, it will not work by importing the models one at a time and making a new layer for each model, right?
-
Hi, I asked about this in the New User's forum and no one seems to have an answer. I want to be able to import a group of models made in Rhino and put each model on a different layer in the voxel room. What I can't figure out is how to get the different models to come out the same relative size and in the same location as they were in the original Rhino file. That way I can sculpt each piece so that it fits correctly with the other pieces near it. Is it even possible to do this in 3D Coat? So far the way I am doing this is to scale the parts by eye and move them around by eye, and since they're organic shapes, it is really hard to get this accurate. Many Thanks!
-
Hi, I'm Dave Nugent and I am a pattern maker, as my user name suggests. I make designs and models and molds and such for using in both sand and lost-wax foundries. Much of the work I do is decorative- for the architectural hardware industry. I'm kind of an old guy, so I started this occupation using all hand methods, like carving wood, modeling clay. Gradually started adding digital methods as they became mainstream. Now, most of what I do I design with Rhino3D and machine by CNC. I played with the Sensable system some years ago, but the price was too much for a one-man operation. 3D Coat looks like it will get the same results, though I still haven't figured out how to deal with keeping objects on multiple layers scaled the same and in the position they were originally designed in when I import them. I think the feel of sculpting with a Wacom tablet VS using a haptic device is not different enough to justify the price difference. Most sculpting seems to be visual rather than tactile. I do think that the fact 3D Coat allows use of 3D Connexion devices makes all the difference in how usable the program is. Well done! Thanks!
-
Hi, I'm new to the forum. My name is Dave, and I make foundry patterns. I'm also new to 3dCoat and need help with this. I have modeled basic shapes in Rhino that will be combined to make a piece for CNC machining. I need to voxel sculpt the parts, then export them back to Rhino so I can program the machining. When I import into 3dCoat, I want to put each piece on a separate layer. I also want the pieces to be the same size relative to each other and in the correct location so I can sculpt each piece so it fits with the pieces near it. I figured out how to put them on their layers and turn them into voxels, but I can't figure out how to make them all come in at their original sizes and original locations. How do I do that? Thanks!